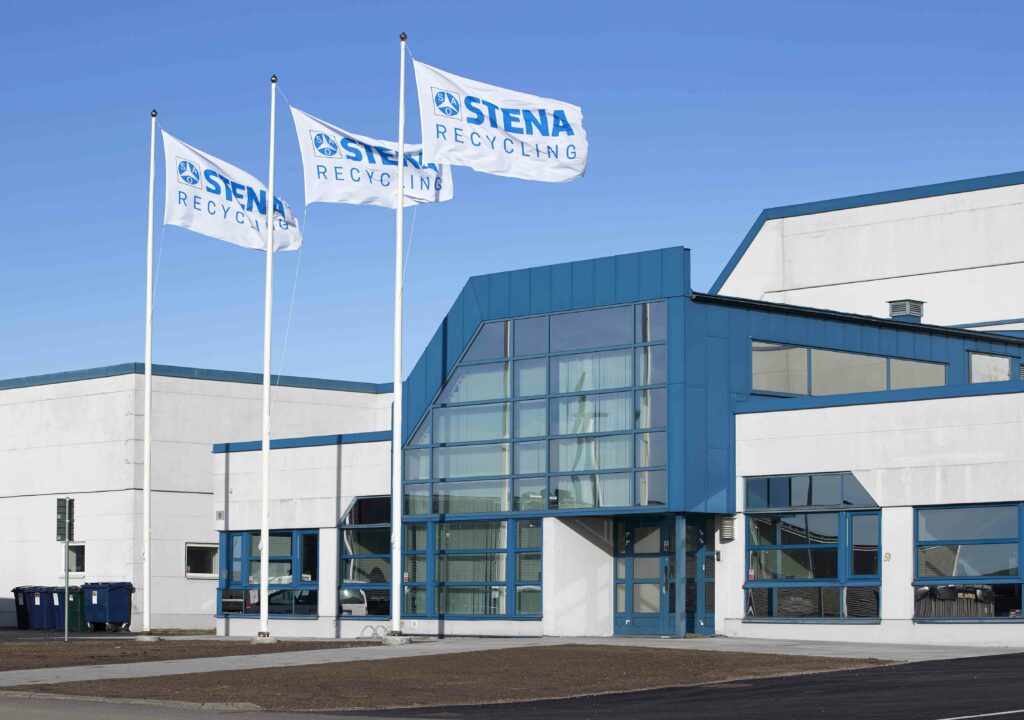
Denne saken sto på trykk i Kretsløpet nr 3-2023
Elbilbatterier og batterier fra mange andre bruksområder kan nå gjenvinnes i Stena Recyclings nye anlegg i Halmstad i Sør-Sverige. Prosessen gjør det mulig å gjenvinne 95 prosent av materialene i batteriene.
AV ASTRI KLØVSTAD
Det er bare en prosent av bilbatteriet som er litium. Men 95 prosent av dette skal gjenvinnes. Det skal også de andre materialene som batteriet er bygget opp av. Prosessen til Stena Recycling består av tre faser, hvorav anlegget i Halmstad utgjør den midterste.
Fase 1 er nemlig desentralisert til Stena Recyclings oppsamlingsanlegg for brukte batterier. Slike anlegg finnes det stadig flere av i Sverige, Danmark, Polen, Finland og Tyskland og de er under bygging i Norge og Italia. For Norges del kommer det første anlegget på Stena Metalls område på Ausenfjellet i Lillestrøm kommune. Det skal stå klart til mottak av batterier før jul.
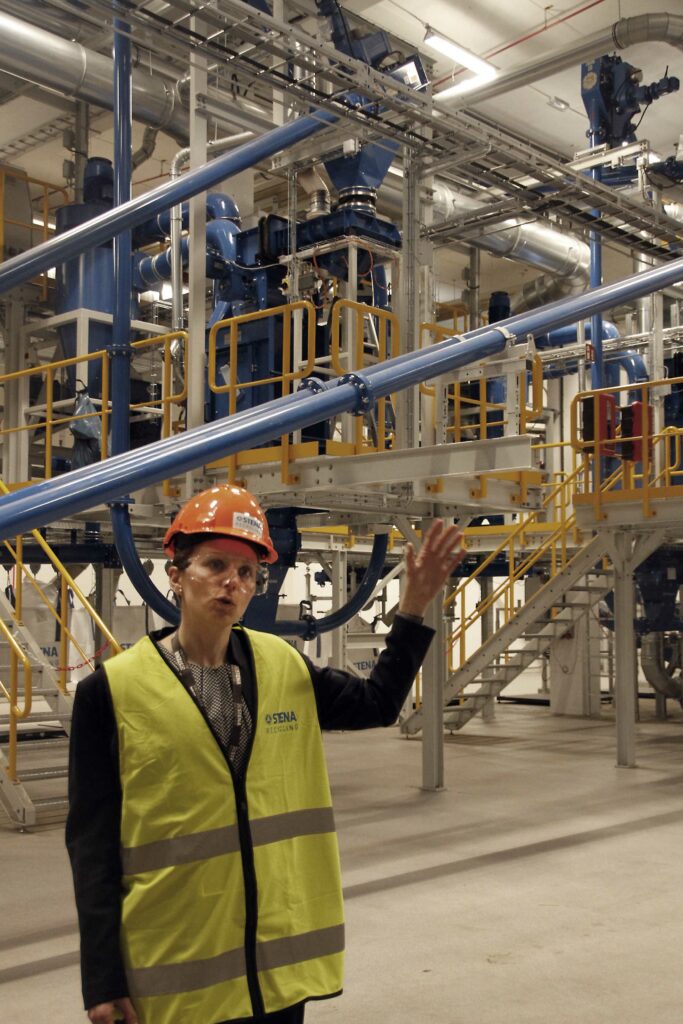
HELSESJEKK AV BATTERIENE
I fase 1 blir batteriene vurdert for ombruk. De har ikke lenger kraft nok til å drive en bil, men om de er uskadd og i orden, kan de plasseres i såkalte energilager der strøm fra for eksempel soleller vindkraftanlegg kan oppbevares til dager da sola ikke skinner eller vinden ikke blåser. Batteriene lades ut og lades opp igjen gang på gang for å kartlegge kvaliteten på dem. Er de for dårlige, eller om de er skadet på noe vis, blir de ladet ut og sendt til fase 2.
– Ved utladningen blir energien ført inn på elektrisitetsnettet og brukt i vår egen prosess. Etter utladning pakkes batteriet ut og demonteres i sine enkelte moduler for å oppnå høyest mulig resirkuleringsgrad. Vi gjenvinner materialene i coveret og i kablene – som plast, kobber og aluminium – lokalt. Det muliggjør sikrere og mer kosteffektiv gjenvinning. For batteripakker med god design for resirkulering er denne utpakkingen mye enklere og mer kostnadseffektiv enn for batteripakkene som er limt og festet sammen med komplekse løsninger. Det fortalte Carina Petersson som er sjef på anlegget i Halmstad under omvisningen i forbindelse med åpningen av anlegget i slutten av mars.
INN I KVERNEN
Når batteriene er utladet og kortsluttet blir de altså sendt til Halmstad og kan tas inn i prosessens fase 2, hvor første trinn er en kvern. Før det kjøres inn i kvernen blir de ulike materialene separert til ulike batcher. Det gjøres for å få renest mulig sluttprodukt, men også for å kunne følge de enkelte batteriene gjennom hele prosessen. Det er nemlig ny lovgivning på trappene som blant annet krever full sporbarhet for alle batterier gjennom hele prosessen, og dette er det tatt høyde for her.
Selv om batterimodulene nå er uten strøm er det likevel en risiko for at det kan oppstå brann i kvernen. – Vi har tre uavhengige systemer for å håndtere brann. Det første er at vi ved hver batch stenger kvernen og fyller den med nitrogengass for å fjerne oksygenet. Vi har også et automatisk system som kan slokke branner om det skulle oppstå, og den siste løsningen er at vi kan fylle hele kvernen med vann, fortalte Petersson.
TØRKEPROSESS MED GJENVINNING AV ELEKTROLYTT
Etter at materialet er malt i kvernen, utgjør det en bløt masse siden batteriene inneholder flyktige stoffer, løsningsmidler og flytende elektrolytt. Dette er brannfarlig og i en tradisjonell gjenvinningsprosess ville dette blitt brent bort. Her er det isteden tatt sikte på å gjenvinne også elektrolytten, og neste trinn i prosessen er derfor en tørking. Materialet sendes inn i en stor sylindrisk trommel som fungerer som en stor tørketrommel. Inni denne lages det vakuum, og så varmes materialet til mellom 80 og 180 grader. Da fordampes elektrolytten og dampen transporteres inn til neste rom der den kondenseres ned til flytende form igjen. På den måten får man ut elektrolytten som et gjenvinningsmateriale. Resten av gassen renses for ikkeorganiske stoffer i en gass-scrubber, før de siste organiske stoffene brennes bort i et etterbrenningskammer. Etter det skal det bare være ren luft som slipper ut.
– Vi har kapasitet på 10 000 tonn batterier per år, og det er dette som er det begrensende steget, dette er flaskehalsen. Men vi har dimensjonert det slik at man kan installere en slik stor tørketrommel til, og om vi gjør det kan vi doble kapasiteten til 20 000 tonn direkte, sier Peterson. 10 000 tonn batterimateriale betyr egentlig 15 000 tonn elbilbatterier, siden det som er av rene materialer som plast, aluminium og kobber allerede er plukket av.
FARLIG STØV
Etter at materialet er tørket, transporteres det til separerings- og sorteringshallen. Her er det også fare på ferde, men nå er det ikke brann som er den store trusselen.
– Dette er svært giftig materiale, det består av tungmetalloksider, nikkel og koboltoksider. Kobolt er kreftfremkallende. Det er også fare for støveksplosjoner fra grafitten. Dette materialet er veldig skadelig for helse og miljø så hele anlegget er konstruert støvtett, fortalte Petersson.
Da anlegget ble åpnet med brask og bram den 30. mars og Kretsløpet og annen presse og gjester fikk omvisning i lokalene, var anlegget ennå ikke startet opp. Alt var rent og pent og big-baggene var tomme. – Når vi starter opp må alle våre medarbeidere som skal inn i anlegget ha friskluftsmasker og en spesiell drakt på seg. Og vi kommer til å måle luftkvaliteten hele tiden. Hvis vi kan forsikre oss om at luften der inne er så bra at det er ok å gå uten dette sikkerhetsutstyret, så kan man gjøre det. Men før man har verifisert det kan man ikke komme inn som besøkende og man kan ikke gå uten verneutstyr, forklarte hun.
En buffersone med et lager som skal inneholder 60 m³ materiale skal holde de forrige og de neste produksjonstrinnene gående i situasjoner hvor man må foreta vedlikehold eller får en uforutsett stopp.
SEPARERING
Materialet er nå tørt og homogent i størrelse. Fra bufferen blir det sendt inn i et nytt prosessverk. Her blir det dannet pellets av aluminium, kobber og plast, og det blir separert ut såkalt black mass som er en blanding av grafitt og verdifulle batterimaterialer; litium, kobolt, nikkel og magnesium. Etter å ha passert gjennom denne mølla, går den svarte massen rett i storsekker, mens de tre andre materialene blir delt etter størrelse i tre separate linjer som er mer eller mindre like. Inndelingen etter størrelse gjøres fordi separasjonsprosessene går bedre om materialet er i nokså like store fragmenter. Alt er forseglet og tett – til og med maskinene og storsekkene er tette – for å hindre støvet i å komme ut i omgivelsene.
I siste del av batterigjenvinningsprosessen sorteres aluminium, kobber, jern og plast ved hjelp av ulike prosesser som Stena har utviklet, testet og brukt i flere år på andre anlegg på Stena Nordic Recyclingsenter i Halmstad. Materialet kommer ned i storsekker, og når de er fulle, tas de ut, merkes for sporbarhet, kjøres på lager og er klare til å lastes til kundene.
VIDERE TIL FASE 3
Men hva med litiumet? Og de andre verdifulle materialene? Jo, de går videre i form av black mass til fase 3. Den foregår hos partnere som gjennom en hydrometallurgisk prosess separerer litium, nikkel, kobolt og magnesium og gjør dem til råmateriale for nye litiumbatterier. Alle storsekkene med blackmass får samme type sporbarhetsmerking som batteriene har hatt med seg hele vegen.
– Hele prosessen er veldig automatisert. Den kommer til å bli styrt fra et kontrollrom der våre prosessoperatører vil kunne styre kvernen, tørken og også vil kunne overvåke hele dette området. Som en ekstra sikkerhetsforanstaltning er det undertrykk i lokalet for å sikre at det ikke blir noen lekkasje av materialet ut. Og det er prosessventilasjon som hele tiden plukker ut det eventuelle spillet så blackmassen havner i sekken, fortalte Petersson.
Stena Recycling har investert 275 millioner svenske kroner i batterigjenvinningsanlegget i Halmstad og samtidig investeres 100 millioner i oppsamlingssentraler i Europa. Selskapet fikk 70,7 millioner kroner i støtte fra Energimyndigheten i 2021. Marcus Martinsson, Stena Recyclings produktområdesjef for batterier, håpet ved innvielsen at anlegget ville få oppstart i midten av april, men anslo at det vil ta to år før man er oppe i full produksjon.
FLERE FABRIKKER KOMMER
– Vi har alt for lite batterier med tanke på hva vi kommer til å trenge når vi er fullt elektrifisert. Hvert år kommer Europa til å sette noe sånt som 15–20 millioner tonn litiumionbatterier på markedet. Det kommer til å være helt nødvendig for den grønne omstillingen. Og vi har bare så vidt begynt den reisen. Det kommer skjerpede krav fra EU som sier at ingen får selge batterier på markedet uten at de kan dokumentere at så mye av kobolten, litiumet, nikkelen og kobberet er gjenvunnet. Det er kjempesmart. EU kan jo bare påvirke EU, og ikke Kina og Amerika. Men om de vil selge til Europa, må de oppfylle kravene, sa Martinsson og la til at det ikke bare kommer krav om hvor mye vi gjenvinner, men også på hvordan vi gjenvinner materialene. – Vi må kunne gjøre rede for CO2-avtrykket for hele prosessen, og vi må kunne dokumentere hvor mye av litiumet vi faktisk klarer å hente ut av disse batteriene.
– Eierfamilien til Stenakonsernet har sagt at så fort vi har fylt dette anlegget, så bygger vi et nytt. Vi skal følge markedet. Og det er klart, setter vi 15–20 millioner tonn batterier på markedet hvert år, kommer det før eller senere 15–20 millioner tonn tilbake, og da kommer vi ikke vi så langt med et anlegg for 10 000 tonn, slo han fast.